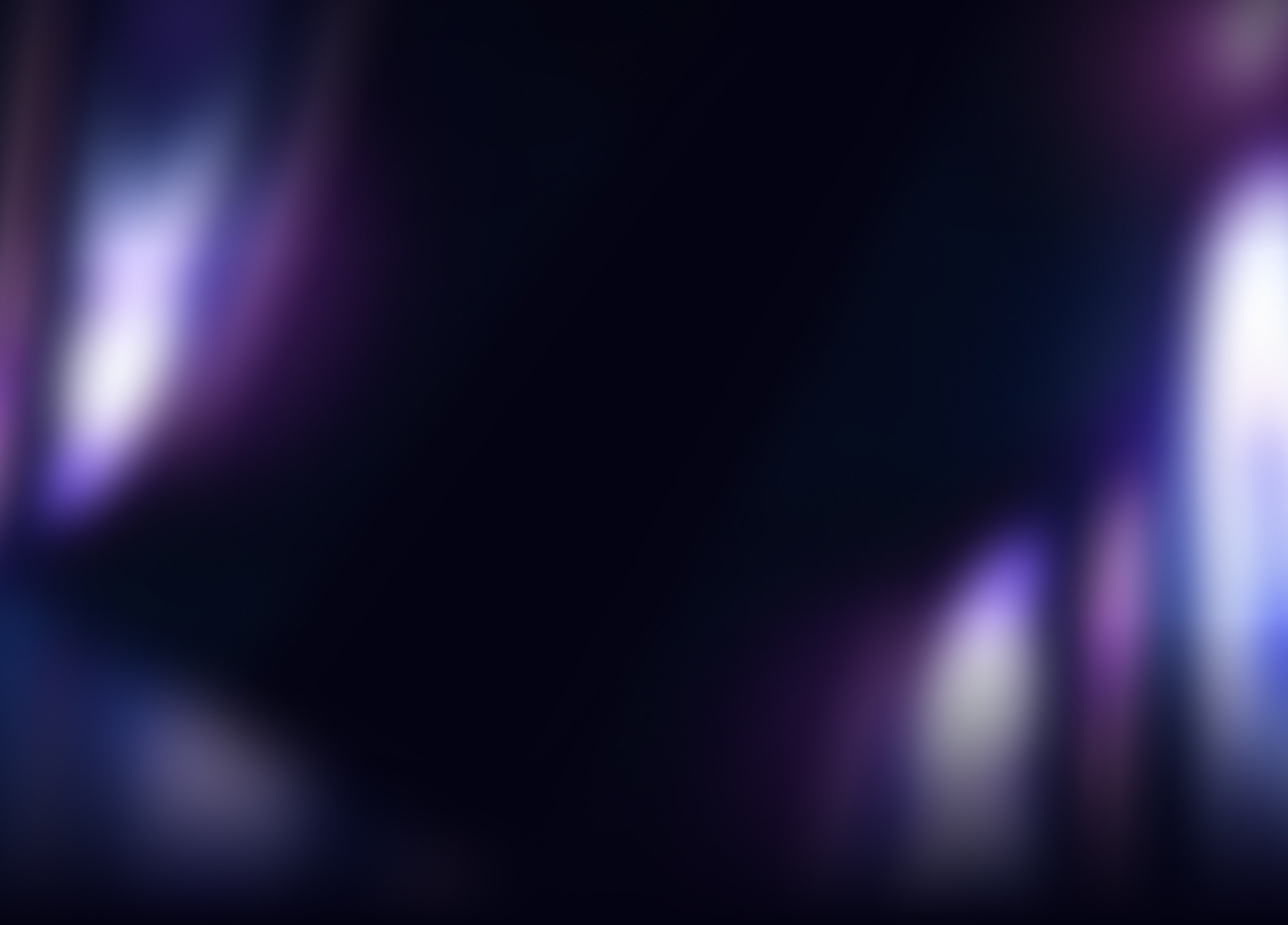
Dec 3, 2024

Introduction
In a globalized and competitive market, operational efficiency is a critical differentiator for success. Process optimization enables businesses to boost productivity, reduce costs, and deliver higher-quality services, laying a strong foundation for sustainable growth. This article explores what process optimization is, its benefits, implementation steps, and practical examples.
What Is Process Optimization?
Process optimization involves mapping, analyzing, and improving workflows to eliminate inefficiencies and maximize results. This can include restructuring tasks, adopting technologies like automation, or applying methodologies such as Lean and Six Sigma, which focus on waste elimination and continuous improvement.
Benefits of Process Optimization
Increased Efficiency
Eliminating redundant steps and automating repetitive tasks allows teams to accomplish more with fewer resources. For example, automating data entry frees up time for strategic activities, boosting overall productivity.
Cost Reduction
Optimized processes minimize waste, such as time, materials, or labor, leading to significant cost savings. These savings can be reinvested into areas like innovation or expansion.
Improved Quality
Standardizing processes ensures consistency, reducing errors and enhancing the quality of products or services, which is vital for maintaining market competitiveness.
Enhanced Decision-Making
Optimized processes generate clear, reliable data, providing valuable insights for strategic decisions based on performance reports or productivity analyses.
Customer Satisfaction
Streamlined processes lead to faster deliveries and higher-quality services, increasing customer satisfaction and loyalty, which are crucial for retention.
Competitive Advantage
Businesses with optimized processes can respond more quickly to market changes, staying ahead of competitors and seizing new opportunities.
How to Implement Process Optimization
Implementing process optimization involves several key steps. First, map current processes by documenting each step to understand workflows. Second, analyze these processes to identify bottlenecks, redundancies, or inefficiencies using tools like flowcharts. Third, redesign processes to eliminate waste and create more efficient workflows. Fourth, implement changes by training teams and adopting necessary technologies. Finally, monitor performance continuously, making adjustments for ongoing improvements.
Tools and Techniques
Several tools and techniques aid process optimization. Lean Manufacturing focuses on eliminating waste, such as unnecessary time or resources. Six Sigma reduces variability and defects for greater consistency. Robotic Process Automation (RPA) automates repetitive tasks like data entry. Enterprise Resource Planning (ERP) systems integrate business processes, such as finance and HR, for enhanced efficiency.
Success Examples
A manufacturing company might reduce production time by 30% using Lean methodology by eliminating unnecessary steps. A service-based business could improve customer satisfaction by 20% by optimizing its support process, ensuring faster and more personalized responses.
Conclusion
Process optimization is essential for businesses aiming to stay competitive in today’s market. By investing in continuous improvement, organizations can achieve greater efficiency, reduce costs, and enhance customer experiences, paving the way for long-term success.